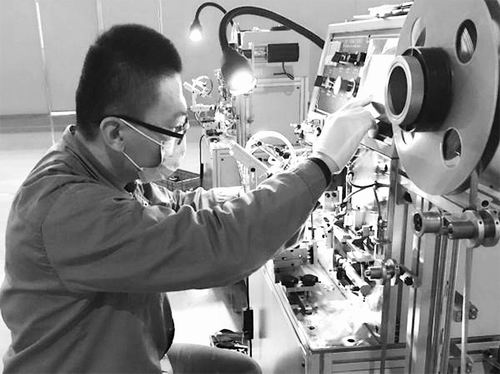
工程师盯着测厚仪实时显示的厚度数据。
■本报记者 沈春蕾 通讯员 王雪珍
高温熔融合金变成带材是在千分之一秒内完成的,每一炉生产出数万米长的整条带材,各处的厚度只允许有两微米的偏差,一丝马虎就可能造成上万米材料的报废。
日前,在宁波中科毕普拉斯新材料科技有限公司(以下简称中科毕普拉斯)的生产车间里,工程师和工人们正热火朝天地忙碌着,新型高饱和磁感强度非晶纳米晶超薄带材,正以每秒20多米的速度从1400oC 的熔融合金中被高速抽出,形成仅有20 微米厚的超薄带材,同时又米秒不差地被同步卷绕成带材卷。
目前,上海蓝沛新材料公司以中科毕普拉斯非晶纳米晶超薄带材为原材料制备的无线充电导磁片,已通过多家手机品牌无线充电验证,并已进入国际著名手机品牌供应链体系。
2015年9月,来自中国科学院宁波材料技术与工程研究所(以下简称宁波材料所)的一支博士团队创立了中科毕普拉斯,并推动新型材料走出实验室。
三人创业组
2003年9月,同窗近十年的门贺和郭海,在大学毕业之后又共同来到日本东北大学金属材料研究所攻读博士学位。日本东北大学金属材料研究所是引领全球非晶纳米晶合金研究的旗帜性研究机构。
当时,我国对铁基非晶合金带材的需求逐年快速增长。但国内量产的非晶合金带材,在质量和产量方面均未达到应用要求,助长了日本公司的非晶纳米晶合金带材以垄断高价大量销往我国。
在日本东北大学从事高性能非晶纳米晶合金研发的门贺和郭海,时刻关注着国内非晶合金产业受日本打压的艰难发展历程,并在心底默默埋下了一颗种子:一定要做出超越日本的高性能非晶纳米晶合金材料。
在完成博士学业后,门贺和郭海分别于2010年和2011年回国加入宁波材料所,门贺主要从事高性能新型非晶纳米晶合金基础研究,郭海在宁波材料所与江苏奥玛德新材料公司共建的非晶软磁合金材料工程技术研究中心,主要从事工程化技术开发,进行非晶纳米晶合金带材及后端应用产品铁芯的产业化技术攻关。
2013年初,即将从中国科学院物理研究所获得博士学位的霍利山,本愿是进入企业从事非晶合金的产业化应用研究,但国内非晶材料行业龙头企业认为他的研究背景与企业研发方向不符,而中小企业与他的研发理念相差太大。
委曲求全还是坚持理念?霍利山遇到了门贺。“你的理念我很认同,如果真有勇气和毅力坚持下去,我们自己可以创建一个非晶合金研发和生产的企业。”门贺的这句话激发了霍利山内心的创业梦想,一毕业后者就去了宁波材料所。
在2014年5月一场国内非晶产业峰会上,3天峰会期间,门贺、郭海和霍利山3个人每天都在会议结束后畅聊到凌晨。那场产业峰会结束时,三人的创业组合基本成型:门贺作为技术带头人负责把控经营方向、资源整合和公司整体管理,郭海主管产品生产、品质管理和市场开发,霍利山负责技术研发、知识产权布局和科技项目管理等。
走出矛盾境地
“虽然我们有自主知识产权且性能优异的材料、意志坚定和优势互补的创业团队、感兴趣的天使投资人,但要开启创业之旅依然异常艰辛。”门贺告诉《中国科学报》,创新型基础材料的产业化不可能像互联网项目、商业模式创新项目那样,投入资金后短期就能见效。
中科毕普拉斯创业团队意识到,新型材料从实验室走向市场,需要经过小试、中试、批量化生产及后端应用产品的开发定型和市场推广等环节,且缺一不可。
尽管不少投资人对新型高饱和磁感强度非晶纳米晶合金带材的产业化感兴趣,但中科毕普拉斯创业团队只是在实验室完成了公斤级小试制备,离规模化生产和销售还有很长的路要走。
“有的投资公司在初轮尽职调查之后便没有了下文。”门贺回忆道,当年我们的新型非晶纳米晶合金,在传统的带材产业化生产设备上很难制备成功,必须要针对自己的新型合金的特点进行专用生产设备的设计、研发和制造。
这让中科毕普拉斯创业团队陷入了矛盾的境地:没有资金投入,便无法制造适用于新型带材生产的设备,也就不可能进行新型合金带材中试试验;而不完成新型合金带材的中试试验,又很难吸引风险投资。
面对这一境况,中科毕普拉斯创业团队在不断完善新型合金制带工艺、开发宽幅带材核心制备技术的同时,坚持与一家又一家投资公司进行一轮又一轮的协商和谈判。
随着商业计划书越来越充实,实施方案越来越具体翔实,投资意向也逐渐明确了下来。在中科毕普拉斯创业团队和宁波材料所技术转移部的共同努力下,创业团队最终打动了宁波榕恒投资管理公司的毛海余和欧阳文生两位合伙人。
对于项目存在的风险,投资人只说了一句话:“万一不成功,就算是为科研事业做贡献了。”这也让中科毕普拉斯创业团队暗下决心,要对得起投资方的信任。
争取合作自己上
2016年10月,中科毕普拉斯创业团队开始设计和制造恒压力制带机组,因遭遇零部件加工困难,工期拖后了将近两个月。“眼看着距离日本东北大学技术团队前来参观和考察的日子越来越近,而制带机组顺利运行是合作洽谈成功的前提条件。”门贺说。
时间紧、任务重,中科毕普拉斯的3位创始人领着入职公司不到一个月的工程师和工人们,一头扎到了设备安装的第一线。加班加点、马不停蹄,制带机组总算安装好了。
但在机组调试时,又出现了新问题:由于是非标设备,设备加工企业一时竟找不到熟练的程序调试员和机组调试员。
没有程序调试员,霍利山自己啃起了自动化程序,协助进行自动控制程序的调试和修改,尽量缩短程序调试周期;没有机组调试人员,郭海穿上防护服戴上面罩,带领毫无制带经验的工程师和操作工进行制带调试。
经过近两个月百余次尝试后,用于调试机组的传统合金带材质量逐渐稳定下来,达到了市售商用带材的标准,在线卷取系统也实现正常工作。
至此,中科毕普拉斯创业团队自己研发、设计和制造的恒压力制带机组可以交付生产一线使用了。
“正是因为在制带机组安装时就深入一线,加深了对设备的实践认识,所以在日后新型带材生产过程中出现的许多问题,我们就能很快发现症结所在,并迅速解决问题。那段时间的收获是巨大的。”郭海在回忆时说道。
2017年9月,iPhone新款手机发布,这款手机最大亮点是无线充电。一直以来对无线充电领域密切关注的中科毕普拉斯创业团队,迅速嗅到了一个新的市场机遇。
已经在非晶纳米晶行业崭露头角的中科毕普拉斯,很快进入无线充电模组制造商们的视野。他们提出的要求也很明确:材料在1.2T以上,宽度60毫米以上、厚度20微米以下,同时满足高频(100kHz以上频段)下具有高磁导率。
生产厚度20微米以下超薄带材,对于当时仅有半年多制带技术积累的中科毕普拉斯创业团队来说,无疑是个巨大的挑战。从制带机组制造安装伊始就在这台机组上“摸爬滚打”,并与之“斗智斗勇”的中科毕普拉斯研发团队,好像与这台机组合为了一体,经过一个多月制带工艺的调整,交出了客户满意的样品。
“20微米以下超薄带材,我们可以生产。”门贺说,这也吸引了在无线充电领域有多年技术储备的上海蓝沛新材料公司关注,对方很快便试用通过了中科毕普拉斯超薄带材样品。
通过蓝沛与中科毕普拉斯的垂直整合,双方初步实现了共赢。
(原文发布于2019年12月12日《中国科学报》第6版)
【原文链接】http://news.sciencenet.cn/sbhtmlnews/2019/12/351956.shtm?id=351956
|